Custom Products
Whatever your rubber injection equipment needs, from single to turn-key production lines, US Molding Machinery can help.
We can custom build our presses to meet any special requirements or specifications you may have.
Below are a few examples of custom presses we have built.
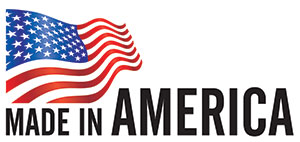
Custom Low Profile
FIFO Vertical Press
Clamping Forces
300 tons
Inject Volumes
17 oz to 90 lbs
Better Uniformity of Compound Temperature
Simple Reciprocating Screw Design
Fast Compound Changeover
Less Space Required (Ideal for Low Ceiling Heights, Small Foot Print)
Custom Dual
Injection Press
Clamping Forces
500 tons
Inject Volumes
10 lb Standard Vertical Inject
10 lb FIFO Horizontal Inject
Platen Size
36 x 36 inches
Special parting line horizontal inject
Two TCU’s
Special features per customer’s request
Custom Bladder Press
for Tire Industry
Clamping Forces
500 to 2000 tons
Inject Volumes
10 to 100 lbs
Platen Sizes
72 x 72 inches
Auto Bladder Extraction
Air Blow Off Removal System
Special features per customer’s request
Standard & Optional Equipment
- Standard: Full alarm, information and diagnostics displays
- Optional: Alarm history display
- Optional: Remote notification of select alarms
- Standard: Key protected set-up modification access
- Optional: Multi-operator password login access
- Protected shift cycle count reset
- Standard: Inject Transfer mode.
- Standard: Bump Cycles: Number, start delay, mold open, and mold close times are all settable
- Bump after inject before dwell
- Bump after dwell
- Bump during inject (specify start point) (inject resumes after bump cycle)
- Standard: Direct pressure setting for motions
- Standard: Direct speed settings for motions
- Standard: Anti-Double inject monitoring via pressure transducer
- Standard: Automatic hydralock pressure setpoint setting during setup
- Standard: Display of system pressure, hydralock pressure, and flow percentage
- Standard: Display of operational information to aid in troubleshooting
- Standard: Display of alarm information to speed problem identification
- Standard: Heater fault monitoring, broken thermocouple, crossed thermocouples, insufficient temperature rises over time
- Optional: Heater current monitoring
- Standard: Circuit breakers for circuit protection, not fuses
- No single phasing of motors or heaters
- No cost to replace fuses
- No time lost finding replacement fuses
- Always the correct fuse value to protect the circuit
- Standard: Single zone electrically heated top and bottom platens with 1-auxilliary zone
- Optional: Multiple heater zones per platen (customer specified)
- Optional: Additional auxiliary heater zones
- Optional:Customheaterconnectionsystems(customerspecified)
- Standard: Temperature Control Unit (TCU) connection o Standard: 3-Zone TCU, water media
- Optional: 3-Zone TCU, oil media
- Optional: 4-Zone TCU, water media (Cold Runner)
- Optional: 4-Zone TCU, oil media (Cold Runner)
- Other systems per customer specification
- Standard: 5 Zones of temperature control (oil or water)
- Feed screw zone
- Injection barrel zone
- Screw barrel zone
- Injection nozzle zone
- Feed port zone
- Optional: Cold runner systems.
- Optional: Pre-heat oven control and connections
- Optional: Pre-heat oven
- Optional: Pre-heat press
- Optional: Heater current monitoring with limits
- Standard: Multiple emergency stop switches at strategic locations
- Standard: Inputs for gate and guard switches integrated into control functions
- Standard: Physical guards
- Optional: Insulated guards
- Optional: Single or dual light curtains
- Optional: Additional light curtains, brands or control schemes as specified by customer
- Standard: Hydraulic over temperature shutdown of hydraulic system
- Optional: interface to flame detector
- Standard: Two-step power on sequence after emergency stop or main power on
- Press power on push button to restore control power
- Start hydraulic pump
- Standard: Two-hand control actuation (without light curtains enabled)
- One push button control actuation with light curtains enabled
- Optional: Powered guard gates
- Standard: Mechanical top platen locks
- Optional: Hydraulic platen locks (Standard on presses 500 ton or larger)
- Standard: Provision for customer supplied mechanical bottom knock out rods
- Optional: factory installed mechanical bottom knock out assembly
- Optional: Hydraulic top ejector system with settable positions and auto/manual control
- Optional: Hydraulic bottom ejector system with settable positions and auto/manual control
- Optional: Hydraulic core clamp system
- Optional: Hydraulic or pneumatic mold shuttle system (exiting platen)
- Optional: Digital or analog feedback of position
- Optional: Rotary core system
- Optional: Air platens for quick mold changes
- Optional: Mold clamps
- Optional: Mold support arms
- Standard: Proportional pressure and flow system for precise control of system movements
- Standard: Differential pressure gauge to show hydraulic filter condition
- Optional: Electrical switch to monitor and alarm hydraulic filter condition
- Standard: Low oil level switch
- Standard: Oil temperature switch
- Optional: Additional hydraulic valves to control customer specified external functions
- Optional: Secondary pump (single pressure) for additional functions
- Optional: Hydraulic silicone stuffer assembly integrated into PLC controls
- Standard: "L" style screw and inject barrel system
- Optional: FIFO inject system
- Standard: Manual inject back pressure control
- Optional: Proportional back pressure control with multiple settings possible
- Standard: Inject modes
- Volume inject: Standard: mode press injects entire contents of barrel
- Inject pressure mode: press injects until programmed pressure is reached, can also be used in conjunction with multiple stage inject to assure a minimum inject volume
- Proportional inject: up to 10 set points with times and volumes can be set to precisely control the inject profile
- Optional: Proportional Inject valve and extra pressure transducer for more precise control
- Standard: two-stage inject profile
- Optional: 10-stage inject profile for Standard: inject mode
- Standard: Anti-Double Inject monitoring via pressure transducer
- Standard: Automatic hydralock pressure setpoint setting during setup
- Standard: Press is vacuum Ready, with outputs for vacuum pump starter, vacuum solenoid valve, vacuum vent valve, and input for vacuum pressure switch
- Optional: Vacuum pump, valve and pressure switch factory installed
- Standard: 20 Recipe function with alphanumeric naming
- Saves ALL setup parameters for a mold setup
- Recipes are stored in the PLC
- Optional: Increased recipe storage capability
- Standard: “7-Day Heat Timer” allows heaters to start and stop on a programmed basis
- Standard: 14 on and off events
- Set day, hour and minute to turn on and off
- Standard: Allen-Bradley SLC 5/04 PLC with panel view + 12” LCD color keypad monitor
- Optional: Touch screen or specific controls per customer requirements
- Standard: Hour meter and total cycle counter
- Optional: external indicator beacons
- Indicator lights customized as required
- Optional: Air blow off system
- Optional: U.S. Molding Machinery Co. gateway factory network
- Integrate all your presses and gather data to improve your operation
- Optional: Collection of data for SPC
- Optional: Tend graphs of cycle data
- Optional: Modem for remote diagnostics or program modification (no charge for service)
- Platforms
- Ladders
- Work Lights
- Stock Feeder
- Automation
- Paint per customer specification
- Custom options and modifications per customer request